Due to their strength and durability, rigid plastics—including HDPE buckets, PP bottles, ABS parts, and PS packaging—are deeply used in a variety of industries. These same features, however, make hard plastics harder to recycle and dispose of. Plastic recycling machinery so comes in extremely useful.
With a full plastic recycling production line, rigid plastic trash can be collected, processed, and turned into plastic flakes or pellets that can be utilized multiple times in manufacturing. From shredders to pelletizers, the equipment that enable this will be explored in this article as well as their working systems in the recycling process.
Keypoints- Due to their thickness, unequal shape, and potential contaminants—rigid plastics (such as HDPE, PP, ABS) call particular recycling equipment.
- A pre-shredder, granulator, washing system, float-sink separation tank, dewaterer, dryer, optional granulator makes up an extensive recycling line.
- To ensure the great cleanliness of the recycled plastic flakes, the washing system removes dirt, grease, and residues through friction and hot water.
- Automated controls—such to be PLC panels, remote monitoring—raise the recycling plant's efficiency, safety, and 24-day operation.
- Investing in an intensive plastic recycling handle lets you establish reusable plastic flakes or pellets, preserve energy, have high throughput and a modular design.
- Products, building materials, automotive components, and consumer goods can all be administered formed from recycled rigid plastics.
- The type of plastic, degree of contamination, calculated output (plastic flakes/pellets), and size of the facility find the equipment to be utilized.
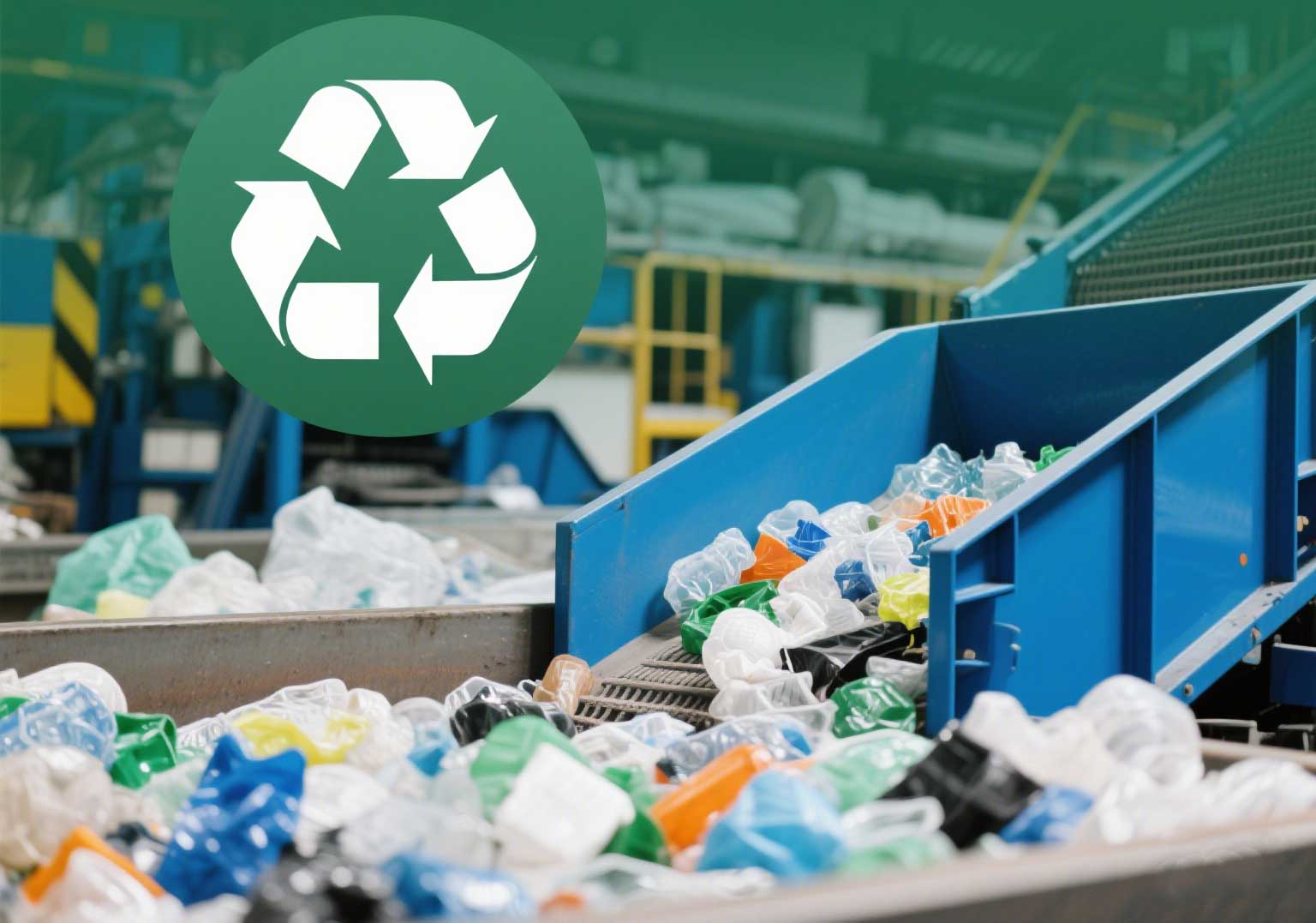
Why Rigid Plastics Require Specialized Recycling Equipment
Rigid plastics are thicker, usually irregular in shape, and can include metal elements, dirt, or coatings unlike soft plastics or bottles. They refer to for heavy-duty recycling equipment able to managing challenging supplies and producing constant output. Advanced recycling facilities guarantee:
The functions of this machinery involve efficient size reduction, thorough washing and sterilization, consistent drying, high-quality reprocessing (pelletizing or flake output), automation, and the capacity to minimize labor with its capabilities.
Overview of a Rigid Plastic Recycling Line
A full-scale rigid plastic recycling system typically includes the following core machines:
1. Pre-shredder or Crusher
Using a pre-shredder or crusher to recycle rigid plastics, such as crates, buckets and containers, these materials will be broken into smaller pieces to make them easier to use.
The initial critical stage in the rigid plastic recycling process is the pre-shredder or crusher. These tools are made to handle thick plastic walls and unusual types.
The hydraulic feeding system and integrated metal detectors enable the extraction of material purity and safety in a wide range of plastic pellets. Because it has blades that are resistant to wear and motors that can be changed to various rates, the shredder has the capacity to keep up its performance even when under heavy-duty conditions. Machines:◆ Twin-shaft shredders
◆ Single-shaft shredders
◆ Heavy-duty crushers
2. High-speed Granulator
The granulator further refines the pre-shredded plastic into uniform particles, thereby optimizing it for drying and washing. With high-speed revolving blades and removable screens, it cuts precisely and controls output size.
Integrating of water-cooled chambers is usual in order to prevent buildup of heat during the processing of plastics, which is especially crucial when working with heat-sensitive materials. Manufacturing of clean, perfectly sized plastic flakes that satisfy high-quality recycling demands requires this machinery.
Machines:◆ Wet granulators
◆ Dry cutting granulators
3. Washing System (Friction Washer + Hot Washer)
Decontaminating the plastic particles relies seriously on the washing system. While hot washers use heated water—often with chemical additives—to dissolve grease, oil, and enduring residues, friction washers brush away dirt, adhesive, and residual labels using high-speed paddles.
All of these methods implemented together ensure that the recycled plastic satisfies the highest standards for cleanliness. Designed for constant operating with low downtime, the washing components—built of stainless steel for durability and corrosion resistance—are created.
Features:Stainless steel build for corrosion resistance
Easy maintenance and access doors
Continuous water ci rculation and filtration systems
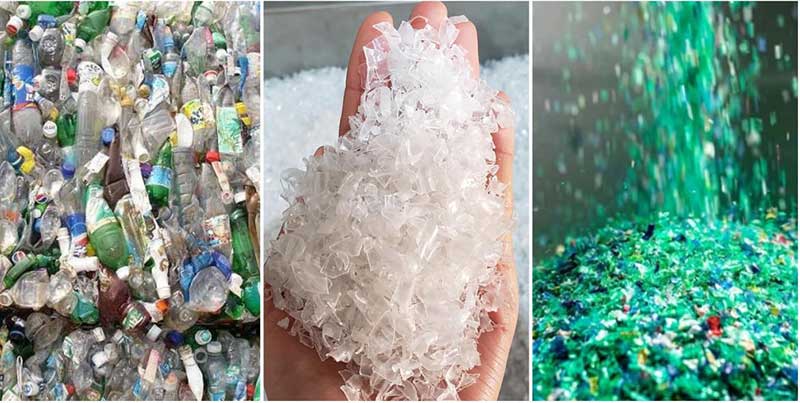
4. Float-Sink Separation Tank
The float-sink tank sorts various types of plastics based on density in order to further clean the recycled material.
In this process, lower-density plastics, such as PP and HDPE, float, while heavier contaminants, such as stones, metals, or PVC, fall to the bottom.
Reliable and energy-efficient, this method lets recyclers properly categorize things. Typically depending on the kind and volume of material dealt with these tanks are adaptable in length and depth.
5. Centrifugal Dewatering Machine
After washing, plastic flakes must be dried before processing. Centrifugal dewatering machines efficiently remove surface water by rotating flakes at high speeds.
It dramatically decreases the drying time and energy application in next periods. Often starring safety covers, discharge channels, and vibration-resistant mounts, these machines offer safe, continuous operation in high capacity settings.
6. Thermal Hot Air Dryer or Pipeline Dryer
From the dewatering unit, this machine takes over to ensure 100% dry flakes. The thermal drier eliminates last moisture from the material by use of a controlled supply of heated air.
Advanced plans call for insulated pipelines to lower heat loss and energy-saving temperature controls. The end is a dry, clean flake perfect for pelletizing or extrusion without giving up quality.
7. Storage Silo or Buffer Hopper
The processed plastic flakes are stored in silos or buffer hoppers for buffering. During the entire line operation, sufficient supply is maintained. Storage hoppers can be equipped with sensors and discharge valves for precise feeding management.
If necessary, they can also be used to mix multiple types of plastic flakes.
8. Pelletizing System (Optional)
A pelletizing equipment can be added to the line's the terminal for plants needing pellet output. These methods repair the dry, clean flakes into consistent plastic pellets.
The line ensures high-purity output armed with pellet cutting heads, filtration systems, and screw extruders. Strand pelletizers, water-ring pelletizers, and underwater pelletizers are the three different kinds of pelletizers that recyclers can choose from according to their specific needs, depending on the material and application. Ideal for ABS flakes, HDPE, PP, PS.
Types:◆ Strand pelletizers
◆ Water-ring pelletizers
◆ Underwater pelletizers
Automation and Control Systems
Intelligent control systems are incorporated to modern plastic recycling lines:
- Programmable Logic Controller panels;
- Touch screen interfaces;
- Auto start/stop systems;
- Emergency shut-off and alarm systems;
- Optional remote monitoring and diagnostics;
These approaches improve broad plant productivity, efficiency, and safety.
5 Facts of Investing in a Rigid Plastic Recycling Line
✅ High Throughput
The equipment can operate 24 hours a day and continuously process tons of plastic waste.
✅ Modular Design
Customize the appropriate production line according to the type of plastic to be processed, the output, and sufficient budget.
✅ High-Quality Output
Plastic flakes or pellets that are clean and uniform and ready to be utilized again and sold again.
✅ Energy Efficiency
These equipments are selected with energy-saving options, which reduce water and electricity consumption during use and adhere to sustainable development.
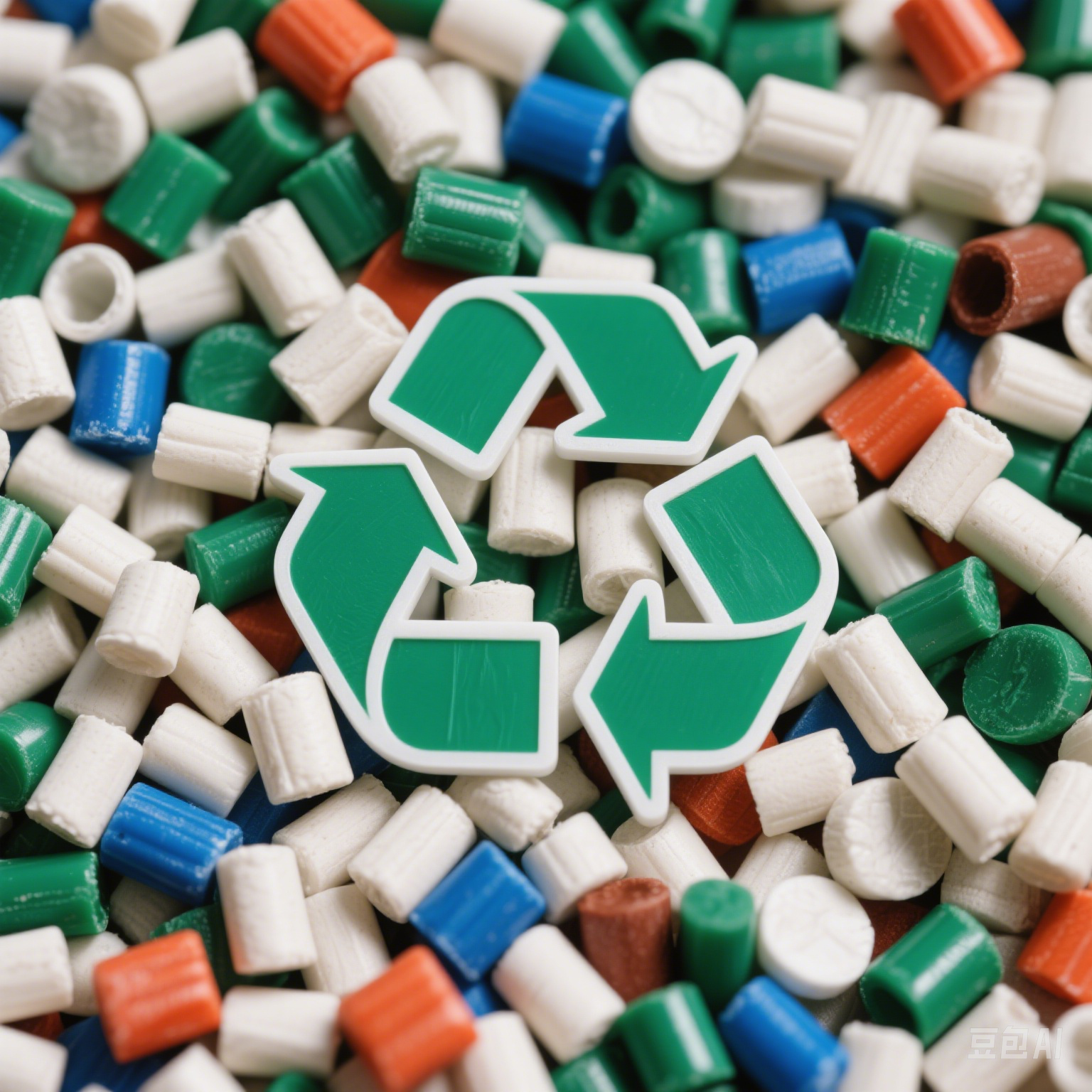
Typical Industrial Applications of Recycled Rigid Plastics
Since recycling machinery requires first place here, it's interesting to note that recycled rigid plastics discover wide usage in:
- Products produced using injection-molds (bins, chairs, cabinets)
- Elements of construction (pipes, panels, fencing)
- Interior panels as well as trims to automotive components
- Consumer goods include flower pots and containers for storage
These uses emphasize the worth and responsiveness of supplying quality recycling proposes.
Choosing the Right Equipment for Your Recycling Plant
If you are intending to process hard plastics, the following ought to be taken into into account:
- A specific type of plastic (such as HDPE, PP, ABS, etc.).
- Raw material shape and size—big drums toward minimal offcuts
- Required output—flakes or pellets
- Level of contamination—food-grade, chemical, etc.?
- Compare small workshops with industrial-scale facilities with regard to of space and capacity
A supplier of recycling equipment with a lot of expertise can help you find solutions that are ideal for your materials, throughput goals, and budget.
Conclusion
Hard plastics are some of the best items for reuse and recycling, but you must have the right equipment to do it. Without the support of an efficient plastic recycling producing line, manufacturers and recyclers may turn hard plastic waste into high-quality, recyclable material. Whether you're building a new recycling plant or upgrading your current one, its operational efficiency and environmental effect depend on the choice of the appropriate machines.
Recycling rigid plastics targets not just for waste reduction but also for the growth of a profitable, environmentally conscious production cycle powered by modern machinery.
FAQs
1. What types of rigid plastics can the machine recycle?
A plastic recycling production line can recycle most rigid plastics including HDPE, PP, PS, ABS, and PC. Typical instances are chairs, containers, crates, buckets, and injected-molded items.
2. Can the recycling line handle plastics with labels or metal parts?
Undoubtedly. Typically, the line comprises in metal detectors and washing systems. The washing and float-sink separation phases enable one to separate labels, adhesives, and tiny metal parts.
3. What is the output size of the recycled flakes?
While the granulator screen size decides the output size, most systems will produce flakes between 10mm and 20mm, fit for pelletizing or reprocessing.
4. How much space is required for a full rigid plastic recycling line?
A common medium-capacity line is suitable for 200–400 square meters. Utilizing modular machines organized either gradually or L-shaped, the layout can be tailored to fit what you have.
5. Do I need a pelletizer for rigid plastic recycling?
Not always. A pelletizer is optional if the goal is plastic flakes for resale or further extrusion. Adding a pelletizing equipment is recommended though, if you wish to produce high-quality plastic pellets for molding or film manufacturing.
6. What is the average output capacity of a rigid plastic recycling line?
The line may handle from 300 kg/h to over 2000 kg/h of hard plastic trash depending on the machine setup. More customized choices are available.
7. How do I choose the right equipment for my plant?
Your budget, the type of rigid plastics you deal with, and your desired output quality—flakes or pellets—will all affect the choice. Professional vendors will offer layout design, equipment guidance, and after-sale support.